Kawasaki’s Bex: A Rideable Quadrupedal Robot Revolutionizing Robotics Mobility
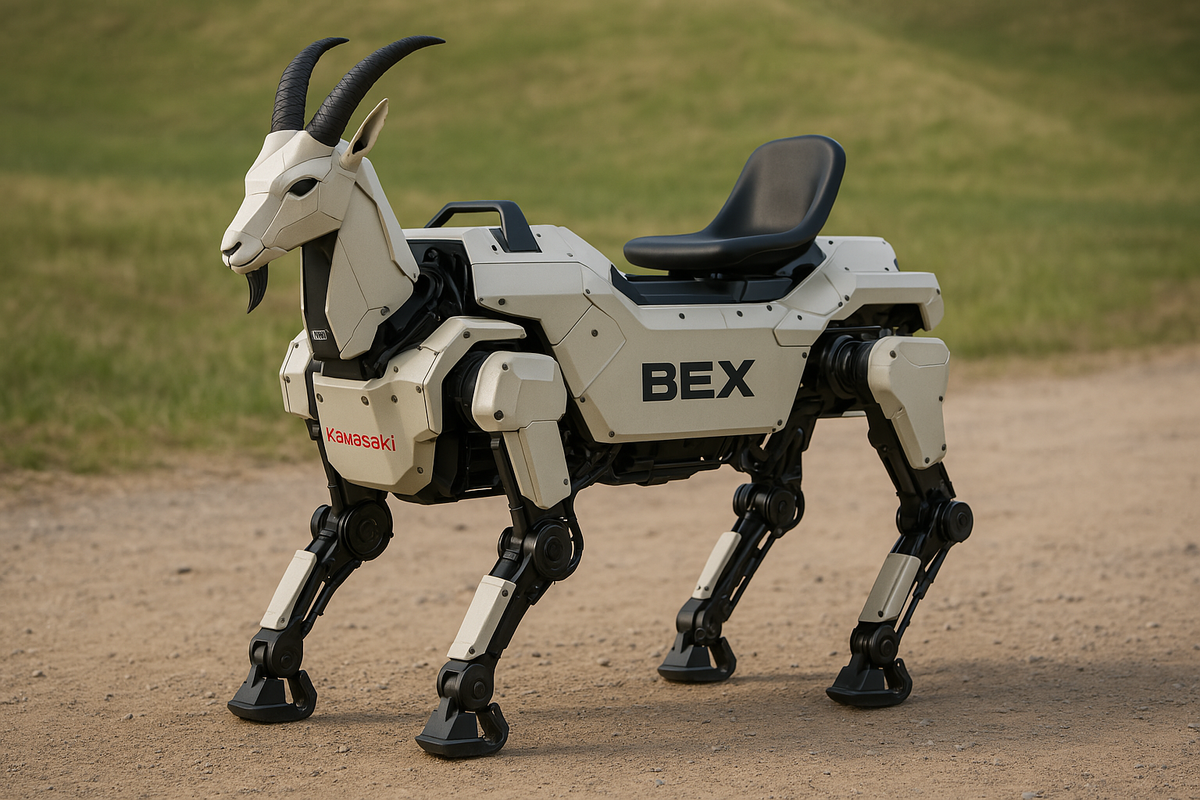
Kawasaki Heavy Industries has unveiled Bex, a rideable four-legged robot inspired by the sure-footed ibex goat. First showcased at the 2022 International Robot Exhibition (iREX) in Tokyo, Bex represents a fusion of Kawasaki’s decades of industrial robotics experience with cutting-edge locomotion innovation. This long-form article will provide an in-depth overview of Bex’s design and features, examine Kawasaki’s journey in robotics that led to this creation, compare Bex to other quadrupedal robots like Boston Dynamics’ Spot and ANYbotics’ ANYmal, delve into the technical innovations and challenges behind its development, and discuss the broader implications and future applications of such a robot. The tone is formal and informative, aimed at tech enthusiasts and industry professionals interested in robotics and automation.
Overview of Bex: Design, Features, and Use Cases
Design and Architecture: Bex is a quadrupedal robot platform modeled after an ibex, featuring four articulated legs and a goat-like aesthetic (including curved horns). Each leg has a jointed structure that allows for walking, and notably, Bex employs a hybrid locomotion system with wheels integrated into its knees. On smooth terrain, Bex can kneel down and roll on these wheels for efficient travel, whereas on rough ground it stands up and walks on four legs – offering the best of both wheeled and legged locomotion. The robot’s body is strong enough to support a human rider, complete with a seat and handlebar interface for direct control. This rideable design makes Bex unique among quadrupeds, effectively blending concepts of a robotic pack animal and an autonomous vehicle.
Key Features and Specifications: Despite its playful goat-like appearance, Bex is engineered for serious tasks. It is capable of carrying up to 100 kg (220 lbs) of payload, either as a human passenger or as cargo. The robot is battery-powered (all-electric) and built on a modular platform – Kawasaki has designed Bex such that the upper body can be reconfigured for different purposes. In the iREX demo, Bex had an ibex-inspired torso and head, but the upper module is interchangeable; it could be outfitted with different attachments or enclosures depending on the use case. Bex’s legs provide it with stability and the ability to traverse uneven terrain, while sensors (such as cameras) mounted on the robot enable remote observation and navigation. Table 1 (below) will summarize Bex’s known specifications alongside other robots for context, including dimensions, payload capacity, speed, and locomotion type.
Intended Use Cases: Kawasaki envisions Bex as a versatile platform for tasks that benefit from a robust, legged robot. Key anticipated applications include: industrial and construction site transport, where Bex could carry tools, materials, or equipment across large worksites; agricultural support, such as ferrying harvested crops or supplies in fields and orchards and infrastructure inspection and patrol, using onboard cameras and sensors to traverse factories or power plants and remotely check gauges and equipment. By combining legged mobility (for navigating rough, outdoor environments or stairs) with wheeled efficiency (for covering flat ground quickly), Bex is positioned as a multi-purpose robot that can operate in environments unsuited to ordinary wheeled vehicles. Kawasaki emphasizes that Bex is an “open innovation platform,” meaning they intend to collaborate with industry partners to customize Bex’s top modules for specific needs (for example, a construction company could add tool-carrying racks, or an inspection-focused Bex might carry advanced sensors). This flexibility in design and function underscores Bex’s role as more than a novelty rideable robot—it is a practical prototype for future service robots that can assist humans in various domains.
Kawasaki’s Journey in Robotics: From Industrial Arms to Quadrupeds
- Pioneering Industrial Robotics (1960s–2000s): Kawasaki has a rich history in robotics, being one of the pioneers in the field. In 1969, Kawasaki manufactured Japan’s first industrial robot, the Kawasaki-Unimate 2000, through a licensing partnership with Unimation. Throughout the 1970s and 1980s, Kawasaki Robotics became known for its industrial manipulators, supplying robotic arms for automotive assembly lines and semiconductor manufacturing. Over 50+ years, the company built a reputation in industrial automation, developing a wide range of robots from small SCARA and articulated arms to large heavy-payload robots. These decades of experience established the engineering foundation—high-precision motors, robust control systems, and reliability standards—that now underpin newer projects like Bex.
- Transition to Service and Humanoid Robots: As robotics technology advanced, Kawasaki began exploring applications beyond factory automation. In the 2010s, recognizing the growing interest in service robots and human-interactive machines, Kawasaki initiated the Robust Humanoid Platform (RHP) program. By 2017, Kawasaki introduced “Kaleido,” a bipedal humanoid robot unveiled at the International Robot Exhibition. Kaleido has since seen multiple generations of improvements (reaching a 7th generation by early 2022) and is aimed at practical human-sized tasks and disaster response. Through Kaleido’s development, Kawasaki engineers grappled with the challenges of bipedal locomotion and balance. According to the RHP project leads, building a reliable two-legged robot proved difficult and highlighted limitations in current technology for humanoids. This realization set the stage for diversifying into other form-factors.
- Genesis of Bex in the RHP Program: Bex was born as an offshoot of the humanoid project. Kawasaki’s RHP team wondered if there was an intermediate solution between complex bipedal robots and simpler wheeled robots. The concept of a quadruped offered a promising compromise: four-legged robots are inherently more stable than two-legged humanoids and better at uneven terrain than wheeled bots, yet potentially easier to develop to a useful stage in the near term. Development of Bex began around 2015 in parallel to Kaleido. The design took inspiration from a sure-footed animal (the ibex) to symbolically represent agility on rough ground. By combining legged locomotion with Kawasaki’s experience in wheeled service robots (the company also worked on an autonomous wheeled service robot named “Nyokkey”), Bex’s creators aimed to cover a gap in the market for a robot that could handle both flat and rough terrains. This history explains why Bex carries features of both a vehicle and a walking machine. In essence, Bex is the result of Kawasaki leveraging its humanoid robotics know-how to build a more immediately practical platform. It embodies the company’s broader strategy to expand from industrial robots into service robots that can coexist and cooperate with humans in everyday environments.
Comparing Bex to Other Quadrupedal Robots
Kawasaki’s Bex enters a growing field of four-legged robots. In this section, we compare Bex with two prominent quadrupedal robots in the industry – Boston Dynamics’ Spot and ANYbotics’ ANYmal – highlighting differences in design philosophy, capabilities, and intended use cases. We will also briefly mention other examples where relevant (such as Boston Dynamics’ historic BigDog and products from companies like Ghost Robotics and Unitree) to contextualize Bex’s place in the quadruped landscape.
- Boston Dynamics’ Spot: Perhaps the most famous quadruped robot, Spot is a nimble, dog-sized robot developed by Boston Dynamics. Spot weighs about 32.5 kg and can carry a payload of 14 kg. It is an all-electric, fully legged design with no wheels, built for agility and autonomous operation. Spot’s strengths include navigating stairs, rough terrain, and even recovering from kicks or shoves, thanks to Boston Dynamics’ advanced control algorithms. Since its commercial release in 2019, Spot has been deployed in various roles: industrial inspection of factories and oil rigs, mapping construction sites, public safety inspections (e.g. hazardous environments), and research. Spot is controlled via a tablet or can follow pre-programmed routes, and it features an array of sensors (cameras, LiDAR options) for perception. Compared to Bex, Spot is much smaller and lighter, which makes it highly agile but also limits its payload. Spot is not rideable and is intended to carry only equipment or sensors. Where Bex emphasizes heavy carrying capacity and a potential for human riders, Spot focuses on dynamic mobility and autonomy. Spot can achieve a top speed of about 1.6 m/s and run for ~90 minutes on a charge, whereas Bex’s speed is lower in walking mode (comparable to a slow trot) but Bex may cover ground faster on wheels. Another key difference is usage: Spot is marketed for autonomous inspection and data collection, whereas Bex is conceived as a modular transport platform. That said, both share some overlap in tasks like industrial inspection, although Bex’s approach to that task would involve carrying heavier instrumentation or even physically transporting items.
- ANYbotics’ ANYmal: ANYmal is a quadrupedal robot developed by ANYbotics (a spin-off from ETH Zurich), designed primarily for autonomous inspection of industrial facilities. In size and weight, ANYmal is comparable to Spot: it weighs around 50–55 kg (depending on configuration) and can carry an additional 10 kg payload (up to 15 kg with reduced performance). ANYmal moves on four legs with no wheels, using powerful actuators to climb stairs and navigate terrain. Its focus is on stability and autonomy; it often carries 3D LiDAR scanners, cameras, and even thermal sensors to detect anomalies in industrial settings. ANYmal’s operating time is roughly 2 hours, and it can automatically return to a charging dock when needed. Compared to Bex, ANYmal is not designed for human riders or heavy cargo – it is more of a sensor platform. Bex’s 100 kg payload capacity far exceeds ANYmal’s, indicating a divergence in purpose: ANYmal is optimized for sensing and inspection, while Bex is built for transportation and carrying loads. ANYmal and Spot both exemplify the current generation of agile, mid-sized quadrupeds used in industry and research, whereas Bex is introducing a new category of a large, rideable quadruped. Bex’s addition of wheels also sets it apart; neither Spot nor ANYmal have integrated wheels (though researchers have experimented with bolt-on wheels for quadrupeds, the designs on the market remain leg-only).
- Other Quadrupedal Robots: Aside from Spot and ANYmal, other notable quadrupeds include Boston Dynamics’ BigDog and LS3, which were earlier (now retired) projects aimed at military logistics. BigDog (introduced in 2005) was gasoline-powered and could carry ~100 lbs (45 kg) over rough terrain, while the later LS3 could carry up to 400 lbs (181 kg) but had reliability issues. Those projects, while demonstrating high payload capability, were exceedingly loud and complex, leading the military to halt further development. Bex can be seen as a civilian analog to the BigDog concept – a quieter, electric cargo hauler with legs – but with modern improvements (like wheels and modular design). Another company, Ghost Robotics, produces legged robots (e.g., Vision 60) primarily for defense; these are similar in scale to Spot and ANYmal and focus on ruggedized, semi-autonomous operation. Chinese companies such as Unitree Robotics have also released smaller quadrupeds (AlienGo, Laikago) for research and hobbyist use; however, none of these smaller platforms attempt the rideable, high-payload role of Bex. This makes Kawasaki’s approach rather distinctive in the current market.
Analysis of Differences: As shown in the comparison above, Bex stands out for its large payload capacity and hybrid movement system, essentially carving out a new niche in quadruped robots—the role of a legged pack mule or riding vehicle. Spot and ANYmal, in contrast, prioritize mobility and sensing over raw carrying capacity. Bex’s design decisions (like adding wheels) sacrifice some of the agility and compactness that Spot/ANYmal have, but they enable new use cases (riding, heavy loads) those others can’t do. In terms of market positioning, Spot has been sold to dozens of companies and research labs, and ANYmal to several industrial clients, whereas Bex is still a prototype not yet commercially available. It will be interesting to see if Kawasaki intends to productize Bex or use it mainly as a research platform. If commercialized, Bex would likely compete in domains like construction or agriculture rather than the inspection niche dominated by Spot and ANYmal. In summary, Bex complements the existing quadruped robots by pushing the envelope in size and capability, demonstrating an alternative path of development focused on load-bearing and human interaction.
Technical Innovations and Design Challenges of Bex
Building a rideable quadrupedal robot like Bex required Kawasaki’s engineers to innovate in several areas and overcome significant technical challenges. This section explores the key engineering aspects – from the novel hybrid locomotion to the structural design for heavy loads – and discusses how Kawasaki addressed (or is addressing) these challenges.
- Hybrid Leg-Wheel Locomotion: One of Bex’s signature innovations is the combination of legged and wheeled mobility. Each of Bex’s four legs is equipped with a wheel at the knee joint. Designing this hybrid system involved solving how to transition between walking and rolling modes smoothly. When Bex encounters flat, even terrain, it can lower its body, essentially squatting down until the wheels contact the ground, and then roll forward on all fours like a wheeled cart. Conversely, when it reaches rough terrain or an obstacle, it must lift itself up and use its legs. The engineering challenge here is ensuring the robot’s stability and control during mode transition – the control system has to manage a change in the degrees of freedom and contact points with the ground on the fly. Kawasaki likely leveraged its experience from wheeled service robots (like the mentioned “Nyokkey”) and legged algorithms from Kaleido to achieve this. The benefit of the hybrid approach is clear: improved speed and energy efficiency on flat ground (wheels are more efficient than legs on flats), combined with the versatility of legs for climbing and uneven ground. However, Bex’s wheels are relatively small (tucked at the knees), so the rolling mode is probably best suited for smooth indoor floors or paved paths. One can imagine the control software deciding in real-time which mode to use based on terrain sensing. Achieving a reliable hybrid locomotion is an active research area in robotics, and Bex is one of the first large-scale examples to implement it in a practical demonstrator.
- Load-Bearing Structure and Balance: Because Bex is intended to carry heavy loads (including a human), its mechanical structure and actuators face unique requirements. Each leg must support a significant fraction of the payload plus the robot’s own weight. Kawasaki’s team has indicated that with four legs, “supporting 160 kg” is feasible, in contrast to a biped like Kaleido where two legs supported ~80 kg. This implies that the motors and gearboxes in Bex’s legs are powerful and robust. A challenge here is to keep the robot’s weight low while reinforcing the legs and frame for strength – a heavy robot can carry more, but then you lose efficiency and put more strain on actuators. The statement that Bex’s payload is nearly double or more its own weight suggests a strong weight-to-payload ratio, if accurate. For example, if Bex weighs ~70 kg and can carry 100 kg, that’s ~1.4x its own weight. In contrast, Spot carrying 14 kg is less than half its weight, and ANYmal’s 10 kg is about 20% of its weight. Engineering a frame and leg joints that can handle such loads repeatedly without failure is a non-trivial task, likely involving high-torque brushless motors, strong reduction gears, and careful material selection (lightweight alloys or composites for the leg links). Balance and center of gravity management are also critical – when a human rider shifts weight or when Bex is loaded with cargo, the control system must adjust to keep the robot stable. Bex presumably uses a statically stable walking gait (like a slow trot or crawl) when carrying heavy loads, to ensure it doesn’t tip. Additionally, Kawasaki might incorporate active suspension or damping in the legs to smooth out the ride for a passenger and reduce shock on the robot’s components. These load-bearing challenges represent a major difference between Bex and smaller quadrupeds and are a testament to Kawasaki’s mechanical engineering capabilities.
- Control System and Human-Robot Interaction: Another innovative aspect of Bex is the inclusion of a handlebar and saddle for a human rider. Unlike most robots that are purely autonomous or remote-controlled via a console, Bex can be physically ridden and steered by a person. This required Kawasaki to implement a user control interface that translates rider inputs into robot motions. The handlebar likely has controls (perhaps motorcycle-like handlebars or a joystick interface) that a rider can use to command direction and speed. Ensuring that a human’s weight shift or sudden movements don’t destabilize the robot would be a key control challenge. The robot might use sensors (like an IMU – inertial measurement unit) to detect its posture and actively balance accordingly. Kawasaki’s background in motorcycles might even play a role here – the idea of a rideable machine with self-balancing elements has some parallels to two-wheel vehicles (though Bex has four legs on the ground for static stability). Moreover, Bex can also be operated without a rider, via remote control or pre-programmed routes, especially for tasks like inspection. Thus, the control system likely has to handle both autonomous navigation (using cameras/LiDAR for obstacle detection) and direct human control. Achieving a smooth blend between these modes, and doing so safely, is a significant software and systems integration task. Kawasaki’s RHP engineers have indicated that they apply walking algorithms from the humanoid project to control Bex’s gait, which would include dynamic balance techniques and gait planning. One can imagine Bex using a statically stable gait (always keeping three legs on ground, for example) when heavy or in tricky terrain, and possibly a faster gait when unloaded on easier ground.
- Modularity and Customization: Bex is described as a modular platform, meaning the upper body can be changed per application. This modularity is a technical design choice that introduces its own challenges. Kawasaki needed to design common interfaces – both mechanical (mounting points, power connections) and logical (communication networks) – between the legged base and any potential upper module. Whether it’s a crop carrying basket, a set of manipulator arms, or a different animal-shaped shell, the leg base should be able to support and power it. This is akin to how a tractor can accept various attachments. The challenge is to ensure robustness and plug-and-play simplicity so that partners can develop custom modules without Kawasaki having to redesign the whole robot. Additionally, Kawasaki must manage weight distribution for any attachment; the base has to keep balance no matter what form the top takes. By offering Bex as an “open innovation platform”, Kawasaki is essentially treating the quadruped base as a product upon which others can build. This forward-thinking approach requires standardization and extensive testing with different configurations to guarantee stability and performance in all cases.
- Power Supply and Endurance: Although specifics haven’t been publicized, Bex’s power system is a crucial technical aspect. Being an all-electric quadruped carrying heavy loads means high energy consumption. We know Spot and ANYmal run ~1.5 hours on a battery; Bex, with larger motors, might need a bigger battery to achieve a useful operating time. Engineers would face the challenge of fitting sufficient battery capacity without making the robot too heavy or bulky. Also, when carrying a human, safety is paramount – the power system must be reliable (no sudden outages causing a collapse). Kawasaki might incorporate redundant power or at least a safe shutdown mechanism to gently lower Bex if battery is critically low. Thermal management of motors and batteries under heavy load is another challenge, especially if Bex is working outdoors in varied climates. These are areas where Kawasaki’s extensive industrial experience helps: designing for reliability, safety, and maintainability. We might expect Bex to have swappable batteries or a fast-charging system if it’s intended for practical use, to minimize downtime.
In summary, Bex’s development required innovation at the intersection of mechanics (leg design, wheel integration, structural strength), electronics (powerful actuators, power supply), and software (hybrid control, balance, user interface). Each of these presented challenges beyond those found in smaller quadrupeds or static industrial robots. Overcoming them positions Kawasaki as a potential leader in this new class of legged robots. The successful demonstration of Bex at iREX 2022 – with a person riding it – suggests that the company has solved many of these challenges in prototype form, although further refinement will be needed to move from demo to real-world deployment.
Broader Implications and Future Applications of Bex
Kawasaki’s Bex is more than just a single robot; it’s a statement about the evolving role of robotics in society and industry. In this section, we discuss what Bex signifies for the future – how rideable quadrupeds might find real uses, how this development fits into larger robotics trends, and what advancements or products we might see next. We’ll also consider the market and societal impact if robots like Bex become commonplace.
Redefining Mobility and Transport: Bex blurs the line between a robot and a vehicle. Traditionally, we think of robots (especially legged ones) as autonomous agents performing tasks independently, and vehicles (like ATVs or tractors) as machines operated by humans for transport. Bex shows a future where a machine can be both: a robot that humans can ride. This has interesting implications for mobility in environments where conventional vehicles can’t go. For example, imagine a ranger in a wildlife reserve or a field worker in agriculture using a Bex-like robot to traverse hilly terrain – the robot could be autonomously carrying equipment most of the time, but the human could hop on and ride it when needed. This dual mode could increase efficiency and reduce fatigue in jobs that involve a lot of walking with gear. Furthermore, for people with disabilities or limited mobility, a rideable robot might one day serve as an all-terrain wheelchair alternative, expanding access to outdoor areas. While Bex is currently a prototype, it sparks discussion about personal transportation robots. If legged robots become reliable and safe, they could form a new category of transport, especially in scenarios where we currently use animals (like pack mules or riding horses) or where roads are not available.
Applications in Industry and Agriculture: In industrial settings, robots like Bex could take on tasks that bridge the gap between stationary robots and human labor. For instance, in construction sites, materials often need to be moved through areas with uneven ground, partially built structures, or debris – conditions where wheeled loaders might not reach and humans carrying loads face injury risk. A robust quadruped like Bex could carry heavy toolkits or construction materials across such terrain autonomously or by following a worker, improving productivity and safety. In agriculture, Bex could be used on farms with terraced fields or vineyards on slopes, carrying baskets of produce or farming equipment. Unlike tractors, a legged robot can step over obstacles and won’t get stuck in mud as easily. The inspection use case is another practical domain: refineries, chemical plants, or power stations often have a mix of stairways and grated floors – a quadruped inspector can navigate these better than wheeled robots. Bex could carry heavier sensor payloads (high-end cameras, robotic arms for manipulation, etc.) to perform maintenance tasks, not just observation. Kawasaki’s push into these applications indicates a broader trend of robotics entering frontline work in outdoor and dynamic environments, not just controlled factory floors. If Bex or its successors prove effective, we could see legged robots becoming standard equipment in certain industries, much like drones have become common for aerial inspection.
Competition and Collaboration in the Robotics Industry: The introduction of Bex also has an impact on the robotics industry landscape. Boston Dynamics, ANYbotics, and others have so far led the quadruped space; Kawasaki’s entry (especially as a large established corporation) adds competitive pressure and diversity of ideas. It’s a sign that the market for legged robots is promising enough that big players are investing in it. Kawasaki’s approach – emphasizing an open platform and partnerships – may drive a more collaborative ecosystem. They have hinted at working with construction or plant companies to customize Bex, which contrasts with more vertically integrated approaches (Boston Dynamics develops everything in-house for Spot). This could accelerate development of specialized robotic solutions. Market-wise, if Kawasaki eventually commercializes Bex, it will likely be in direct competition with other heavy-duty robotics solutions (for example, wheeled autonomous vehicles for mining or construction). Bex might carve out a niche where legs are a must-have, thereby expanding the overall robotics market. It also showcases Japan’s continuing strength in robotics innovation, possibly inspiring other companies to pursue bold concepts.
Public Reception and Ethical Considerations: A robot goat that you can ride naturally captures public imagination. While Bex is mostly framed in practical terms, its almost whimsical design (an illuminated horned “animal” carrying people) can influence how society perceives robots. On one hand, approachable designs like this can increase public acceptance of robots in daily life – people might be more charmed than intimidated by a robotic goat versus an impersonal machine. On the other hand, it raises interesting questions: If robots can replace the functions of animals (like horses or pack mules), what does that mean for those traditional practices? And if a robot is strong enough to carry a person, it must be built with safety in mind – ensuring it doesn’t accidentally cause harm. Regulators and engineers will need to consider safety standards for rideable robots, akin to autonomous vehicle safety, especially if these machines operate near or with humans. Kawasaki’s experience in heavy industry likely means they are attuned to safety, but widespread use of such robots would still require new norms and possibly certifications (for example, one can imagine requiring a “robot operator” license for riding an autonomous robot in public spaces someday).
Future Developments and Innovations: Bex is a starting point, and we can speculate on what future iterations or related projects might look like. Kawasaki or others might develop larger quadrupeds capable of even more weight (for construction or military logistics), or smaller rideable robots for personal use or entertainment (imagine robotic pets that kids can ride at zoos or theme parks). We may also see the integration of arms onto quadrupeds – the IEEE Spectrum article noted Kawasaki mentioning that few quadrupeds have humanoid-like arms. Perhaps a future Bex version could have a manipulator arm mounted on top, allowing it to not just carry but also pick up or manipulate objects, greatly increasing its utility on job sites. Autonomy will also improve: currently Bex can be ridden or remote-controlled, but future versions could have advanced AI to follow voice commands or navigate to waypoints on their own while carrying a load. In terms of design, the concept of wheels on legs that Bex employs might be further refined – maybe retractable wheels, or omni-directional wheels for better maneuvering. Bex’s concept could even inspire new robot forms; for example, other animal-inspired robots (a rideable robotic horse or camel for desert conditions?). Kawasaki’s open-platform stance suggests they expect others to build on their creation, so we might see startups or research groups customizing Bex units for novel purposes.
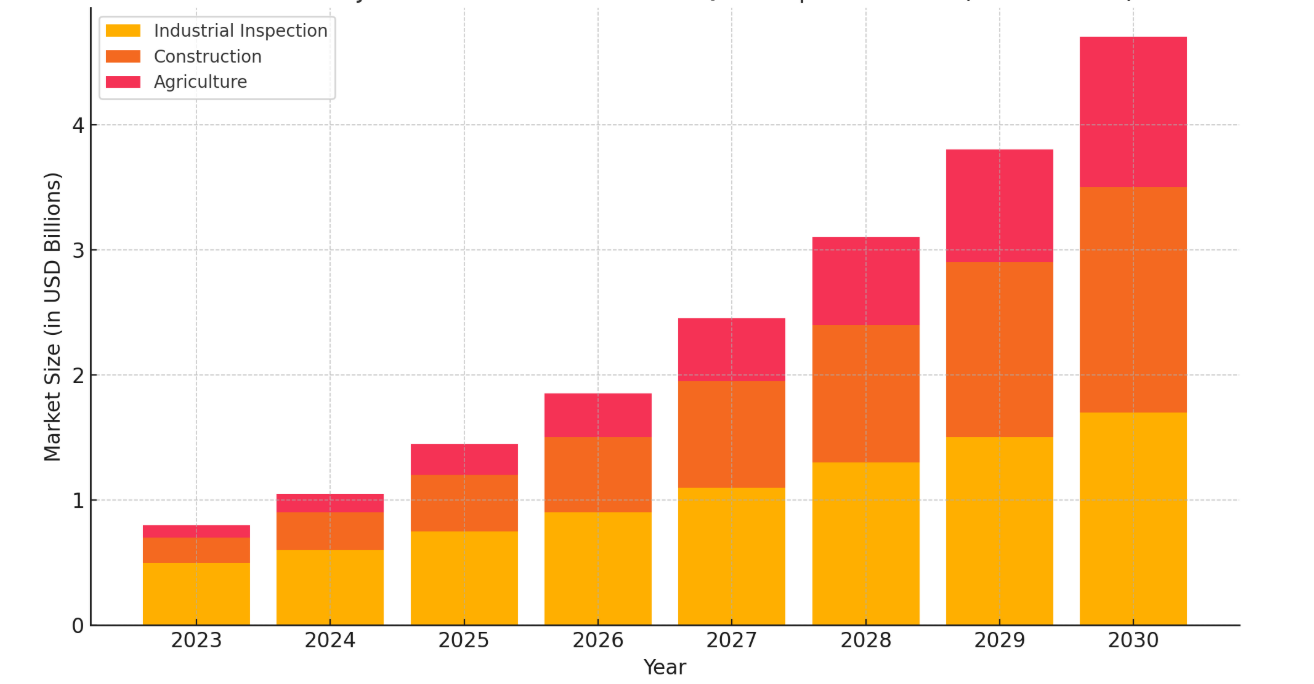
Impact on the Future of Robotics: The broader implication of Bex is that the field of robotics is entering a phase where hybrid solutions and cross-domain innovations are key. Bex combines ideas from humanoid robots, animal locomotion, and even personal transport. This kind of convergence is likely to be a hallmark of next-generation robots. We’re moving past robots that mimic pure human form (which has proven very challenging to deploy) toward robots that selectively combine the best features for the job – in Bex’s case, four legs for stability, wheels for efficiency, an animal-like form for familiarity, and a user interface for direct human control. If Bex is successful, it could encourage more projects that break the mold, leading to a diverse ecosystem of robotic platforms tailored to different tasks yet sharing modular components. For Kawasaki, Bex also positions them in the evolving narrative of robots working alongside humans (so-called cobots in a broader sense, not just industrial collaborative arms). A future scenario might be a team of robots on a construction site: a few Spot-like inspectors, a Bex or two hauling materials, maybe a crane-like robot assembling parts – all coordinated under human supervision. Bex is one piece of that puzzle, focusing on physical interaction and transport.
In essence, Bex’s development and the attention it has garnered show that robotics is not just about incremental improvements to existing machines; it’s about reimagining what robots can do and what forms they can take. The implications range from practical (new tools for difficult jobs) to societal (our evolving relationship with machines). Kawasaki’s venture into rideable quadrupeds could open the door to a whole new category of robots that we might see in the coming decade.
Conclusion
Kawasaki’s Bex robot is an ambitious blend of engineering innovation and practical vision. By taking the form of a rideable, four-legged “robotic ibex,” Bex demonstrates how a half-century of expertise in industrial robots can be applied to create something entirely novel in the realm of mobile robotics. In this outline, we explored Bex’s design – from its unique leg-and-wheel locomotion to its impressive payload capacity – and saw how Kawasaki’s history, from the first Japanese industrial robot in 1969 to the humanoid Kaleido, set the stage for this development. We compared Bex with other quadrupeds like Spot and ANYmal, highlighting how Bex pushes boundaries by focusing on load carrying and human interaction. We also delved into the technical hurdles Kawasaki had to overcome, such as ensuring stability with a rider and managing hybrid mobility. Finally, we discussed the broader implications: Bex could herald new applications in construction, agriculture, and beyond, and it challenges us to envision robots not just as tools or toys, but as partners in both work and mobility.
As robotics enthusiasts and professionals consider Bex, it’s clear that this robot is more than a gimmick – it’s a testbed for ideas that could shape the future of robotics. Whether Bex itself becomes a common sight or its concepts inspire other machines, Kawasaki has expanded the conversation about what robots can be. A rideable quadruped like Bex points to a future where robots carry our goods, help us in daily tasks, or even offer us a lift when the terrain gets tough. It embodies a convergence of robotics sub-fields (legged locomotion, human-robot interaction, modular design) that might define the next era of innovation.
In conclusion, Bex stands as a remarkable example of engineering creativity, one that bridges the gap between science fiction and industrial utility. It encapsulates the excitement in the robotics community as we venture into uncharted territory – building machines that not only mimic biological abilities but also extend human capabilities in new ways. Kawasaki’s Bex invites us to imagine a world where walking robots work alongside people in factories, farms, and wilderness trails, carrying the load and forging a path into the future of technology. The journey of Bex is just beginning, and it will be fascinating to watch how this robotic goat and its descendants contribute to the ever-evolving story of robotics.
References
- Kawasaki Heavy Industries – Bex Official Introduction
https://global.kawasaki.com/en/corp/newsroom/news/detail/?f=20220330_3483 - IEEE Spectrum – Kawasaki’s Robot Goat Bex Can Carry Humans
https://spectrum.ieee.org/kawasaki-robot-goat-bex - TechCrunch – Kawasaki Introduces a Rideable Robot Goat Named Bex
https://techcrunch.com/2022/03/10/kawasaki-unveils-rideable-robot-goat-bex/ - Kawasaki Robotics – RHP Kaleido Project Page
https://robotics.kawasaki.com/en1/solution/rhp_kaleido/ - Boston Dynamics – Spot Robot Overview
https://www.bostondynamics.com/spot - ANYbotics – ANYmal Autonomous Robot
https://www.anybotics.com/anymal/ - The Verge – Kawasaki Builds a Rideable Robot Goat
https://www.theverge.com/2022/3/10/22971497/kawasaki-rideable-robot-goat-bex - Popular Mechanics – Kawasaki’s Bex Robot Goat
https://www.popularmechanics.com/technology/robots/a39404218/kawasaki-bex-robot-goat/ - Interesting Engineering – Kawasaki Debuts a Robot Goat That You Can Ride
https://interestingengineering.com/innovation/kawasaki-robot-goat-you-can-ride - DesignBoom – Kawasaki’s Rideable Robot Goat Bex Walks and Rolls
https://www.designboom.com/technology/kawasaki-robot-goat-bex-rideable-legs-wheels-03-14-2022/