High-Resolution 3D Printing Is Reshaping Metal and Ceramic Manufacturing
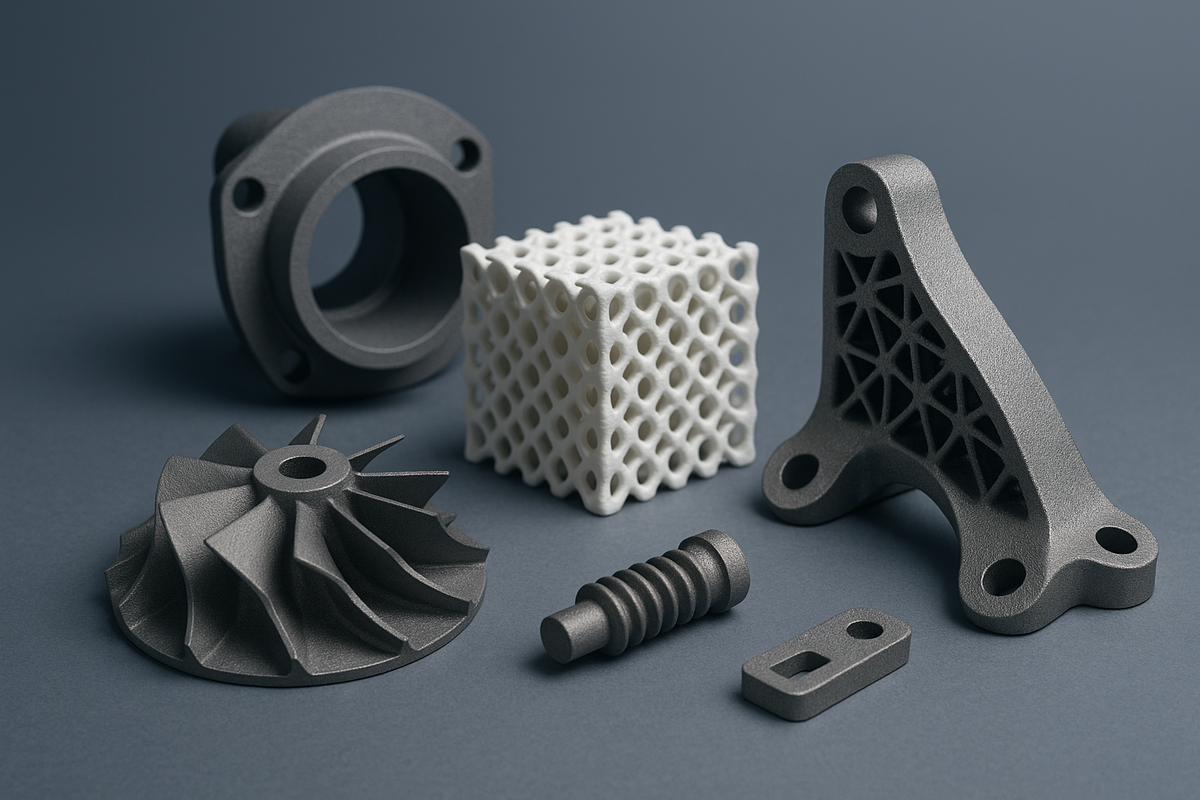
In the realm of advanced manufacturing, the convergence of material science and additive technology has reached a pivotal moment. High-resolution 3D printing for metals and ceramics is not only redefining production processes but also reshaping the strategic possibilities for entire industries. While additive manufacturing (AM) has long been associated with prototyping and plastic components, the rapid development of high-precision techniques capable of fabricating dense, mechanically robust metal and ceramic parts marks a turning point in industrial fabrication.
Historically, manufacturing components made from metals and ceramics has involved subtractive methods—such as milling, grinding, and casting—that are time-consuming, waste-intensive, and restricted by geometric limitations. Metals require complex machining and thermal treatments to meet performance standards, while ceramics, known for their brittleness and high-temperature resistance, pose significant challenges in shaping and processing. These traditional constraints have stifled innovation, particularly in sectors demanding lightweight, thermally stable, and mechanically resilient components.
However, the rise of high-resolution 3D printing is dismantling these barriers. Characterized by layer resolutions in the range of 10–50 microns and the ability to control microstructures at unprecedented levels, new additive techniques allow manufacturers to build intricate parts directly from digital models with minimal waste. This is particularly impactful in industries such as aerospace, medical devices, and advanced electronics, where component complexity, weight reduction, and performance optimization are critical to success.
At its core, high-resolution 3D printing for metals and ceramics combines the design freedom of additive manufacturing with the structural integrity historically reserved for conventionally manufactured parts. By enabling precise control over every layer of material deposition, these technologies allow the realization of geometrically complex parts that were previously impossible—or prohibitively expensive—to produce using traditional methods. Furthermore, innovations in sintering, thermal management, and binder chemistry have made it possible to maintain the mechanical properties required for real-world applications without sacrificing detail or precision.
The implications for design and engineering are profound. With the ability to consolidate multiple components into a single monolithic part, engineers can reduce assembly time, eliminate points of failure, and improve performance. Topology optimization algorithms, paired with high-resolution printing, allow for organic geometries that distribute stress more efficiently while minimizing material usage. The result is a paradigm shift where design is no longer constrained by manufacturability but instead driven by functionality and innovation.
Importantly, the use of metals and ceramics in additive manufacturing expands the scope of application beyond what is achievable with polymers alone. High-temperature ceramics, such as zirconia and alumina, are being used to create medical implants, catalytic substrates, and components for jet engines. In parallel, metals like titanium, nickel-based superalloys, and stainless steel are enabling the production of strong, lightweight structures suitable for aerospace and defense. These materials are not merely replacements for plastics but foundational enablers of high-performance, mission-critical systems.
The evolution of high-resolution 3D printing is also deeply intertwined with broader digital transformation trends across the industrial sector. As manufacturers adopt more agile, data-driven workflows, additive manufacturing serves as a cornerstone of Industry 4.0—offering digital part inventories, rapid iteration cycles, and scalable, distributed production networks. Combined with advances in computational design and artificial intelligence, the potential for mass customization and predictive quality control is becoming a practical reality.
It is within this broader context that the role of high-resolution 3D printing for metals and ceramics becomes truly revolutionary. It is not merely a new tool in the manufacturing toolkit; it is a foundational shift in how objects are conceived, designed, and brought to life. As global competition intensifies and supply chain resilience becomes a top priority, the capacity to produce critical components with speed, precision, and minimal waste offers a decisive advantage.
In the sections that follow, we will explore the technical foundations of high-resolution additive manufacturing, examine real-world use cases across industries, and analyze the economic and environmental impact of these emerging technologies. We will also confront the remaining challenges—ranging from material limitations to workforce readiness—that must be addressed to fully realize the potential of this transformative approach.
The manufacturing renaissance powered by high-resolution 3D printing is no longer speculative. It is unfolding in real-time, promising a future where design complexity is not a limitation but an asset, and where innovation in form and function is bounded only by imagination and material science. This is the new era of manufacturing—precision-engineered, digitally driven, and fundamentally redefined.
Technology Deep Dive
How High-Resolution 3D Printing Works for Metals and Ceramics
High-resolution 3D printing for metals and ceramics represents a confluence of advanced manufacturing techniques, cutting-edge material science, and precise engineering control. This section delves into the key technologies enabling this transformation, the fundamental processes involved, and the innovations that are pushing the boundaries of what additive manufacturing (AM) can achieve with these historically challenging materials.
Overview of Core Additive Technologies
Several additive manufacturing processes have been adapted or developed specifically for metals and ceramics. The most prominent include:
- Powder Bed Fusion (PBF):
PBF encompasses techniques such as Selective Laser Melting (SLM) and Electron Beam Melting (EBM), which utilize focused energy sources to selectively fuse fine metal powders layer by layer. These methods provide excellent resolution—often in the range of 20 to 50 microns—and produce parts with high density and mechanical strength. - Binder Jetting:
In binder jetting, a liquid binding agent is selectively deposited onto a thin layer of metal or ceramic powder. Once the part is fully printed, it undergoes a debinding and sintering process to fuse the particles. While this process typically offers faster build times, the resulting parts initially exhibit lower density and require careful post-processing to achieve final strength. - Stereolithography (SLA) and Digital Light Processing (DLP):
These processes, traditionally associated with photopolymer resins, have been adapted for ceramics through the use of ceramic-filled photosensitive resins. Upon printing, parts are cured with UV light, then thermally debound and sintered. Lithoz, for example, employs a DLP-based process known as LCM (Lithography-based Ceramic Manufacturing) that achieves resolutions below 25 microns and exceptional feature fidelity. - Material Jetting and Extrusion for Ceramics:
Material jetting techniques deposit droplets of ceramic suspensions, which are subsequently dried and sintered. Alternatively, ceramic pastes can be extruded through fine nozzles in a process similar to Fused Filament Fabrication (FFF). Though these methods tend to offer lower resolution, innovations in nozzle control and feedstock rheology are closing the gap.
Each of these technologies brings trade-offs between build speed, resolution, part density, and material constraints. However, when applied correctly, they provide a viable route to fabricating components with geometries and properties unattainable by traditional manufacturing.
Material Considerations and Processing Complexity
Printing with metals and ceramics introduces distinct material-related challenges, primarily due to their physical and chemical properties.
- For Metals:
Key considerations include particle size distribution, oxide layer formation, and thermal conductivity. Fine powders (typically 15–45 microns) must be carefully controlled to ensure even layering and consistent energy absorption. In high-resolution PBF systems, the laser or electron beam must be finely tuned to avoid warping or excessive residual stresses. Post-processing, such as heat treatment and hot isostatic pressing (HIP), is often employed to improve microstructure and reduce internal voids. - For Ceramics:
Ceramics pose a different set of challenges. Unlike metals, they do not melt easily but instead sinter—fusing together under high heat without liquefying. The sintering process must be tightly controlled to prevent cracking, warping, or uneven shrinkage. Additionally, the slurry or resin formulations used in ceramic printing must balance viscosity, particle loading, and photo-reactivity to achieve both print fidelity and structural integrity.
Both material classes require careful consideration of shrinkage rates, which can range from 15% to 30% during sintering. Therefore, accurate modeling and compensation strategies are essential to maintain dimensional precision in the final parts.
Resolution, Tolerances, and Feature Control
High-resolution 3D printing is defined by its ability to create features in the tens of microns range, with tight control over layer thickness, surface finish, and part geometry. This precision is achieved through several interrelated factors:
- Laser/Electron Beam Spot Size:
In PBF systems, the smaller the energy beam, the higher the potential resolution. Modern systems can achieve spot sizes as small as 30 microns, allowing for intricate detailing and fine internal channels. - Layer Thickness:
Reducing the thickness of each printed layer increases vertical resolution. While this improves surface finish and dimensional accuracy, it also increases print time. Typical high-resolution systems operate with layer heights between 10 and 50 microns. - Pixel Density (in Photopolymer-Based Systems):
In SLA and DLP-based ceramic printing, pixel size directly affects lateral resolution. With pixel pitches below 50 microns, it is possible to print highly detailed ceramic microstructures suitable for biomedical and electronic applications. - Support Structures and Orientation:
High-resolution printing demands careful management of support structures, which stabilize complex geometries during fabrication but must be removed without damaging the part. Orientation strategies also impact resolution—features aligned vertically may have different tolerances than those printed horizontally.
Thermal Management and Microstructure Optimization
Thermal gradients during the printing process can lead to internal stresses, warping, and defects. This is especially problematic for metals, where rapid solidification can result in anisotropic mechanical properties or undesirable microstructures.
Advanced machines now incorporate real-time thermal monitoring and closed-loop control systems that dynamically adjust energy input based on temperature feedback. These systems enable consistent microstructures throughout the build volume and reduce the need for extensive post-processing.
For ceramics, controlling the sintering profile—ramp rates, dwell times, and cooling curves—is essential for avoiding microcracking and porosity. Innovations in furnace design and simulation tools have allowed manufacturers to fine-tune these parameters for different ceramic compositions.
Leading Equipment and Platforms
Several commercial platforms exemplify the cutting edge of high-resolution metal and ceramic 3D printing:
- Velo3D Sapphire:
Known for its high-resolution PBF capabilities, the Sapphire system allows for support-free printing of complex metal geometries and fine internal features with high reproducibility. - Desktop Metal Studio System 2:
This office-friendly system uses Bound Metal Deposition and delivers parts with features as small as 0.2 mm and tolerances of ±0.1 mm, suitable for engineering-grade applications. - Lithoz CeraFab System:
Specializing in high-precision ceramic parts, Lithoz’s LCM-based CeraFab systems deliver excellent resolution and surface finish, supporting demanding applications in dental, aerospace, and microfluidics. - XJet Carmel 1400M/C:
Using NanoParticle Jetting (NPJ), XJet systems print both metal and ceramic parts with fine detail and smooth surfaces, eliminating the need for many post-processing steps.
These platforms demonstrate the increasing maturity of the technology, as well as the breadth of available solutions tailored for specific materials and industrial needs.
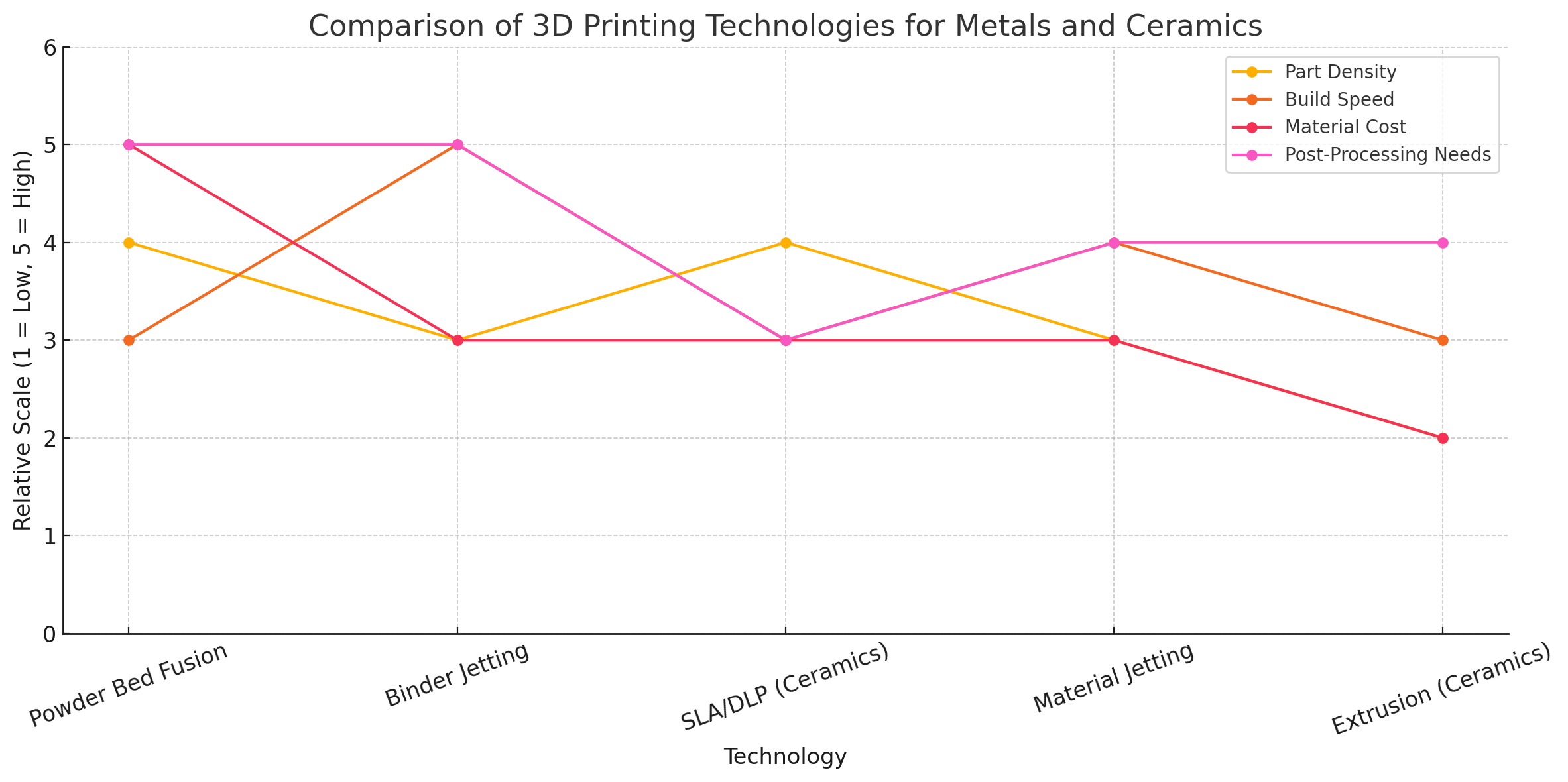
In summary, high-resolution 3D printing for metals and ceramics is built on a foundation of specialized hardware, material innovation, and precision control systems. It requires deep integration between process parameters, material properties, and software algorithms to deliver components that are both geometrically complex and functionally robust. As the technologies continue to evolve, they are unlocking new applications and redefining what is possible in high-performance manufacturing.
Real-World Applications Transforming Manufacturing
The practical impact of high-resolution 3D printing for metals and ceramics is becoming increasingly evident across a broad spectrum of industries. As the technology matures and overcomes initial scalability and material constraints, its adoption is accelerating, driven by the need for lightweight, durable, and geometrically complex components. This section highlights how key sectors—ranging from aerospace to defense—are leveraging high-resolution additive manufacturing to enable breakthroughs in performance, design, and operational efficiency.
Aerospace: Reducing Weight While Enhancing Performance
The aerospace industry has been one of the earliest and most aggressive adopters of high-resolution metal 3D printing, particularly due to its relentless focus on reducing weight without compromising strength. Additive manufacturing enables the creation of complex geometries such as lattice structures, internal cooling channels, and topology-optimized load-bearing components that would be impossible to produce using traditional methods.
High-resolution powder bed fusion systems, for instance, allow engineers to design and fabricate intricate jet engine components, heat exchangers, and lightweight structural parts with tolerances within ±0.05 mm. The benefits extend beyond part performance: consolidating multiple parts into a single monolithic structure simplifies assembly, reduces failure points, and shortens maintenance cycles.
Ceramics also play a critical role in aerospace applications. High-temperature ceramic materials such as silicon carbide (SiC) and alumina are increasingly used for thermal protection systems, nozzles, and insulating components in spacecraft and hypersonic vehicles. With high-resolution 3D printing, these ceramics can now be shaped with precision, offering a combination of thermal resilience and design flexibility that enhances both functionality and mission safety.
Medical and Dental: Personalization and Biocompatibility
In the medical sector, high-resolution 3D printing is enabling the production of patient-specific implants and prosthetics that significantly improve surgical outcomes and patient comfort. Titanium alloys, known for their biocompatibility and mechanical strength, are commonly used to fabricate cranial plates, spinal implants, and orthopedic devices that precisely match patient anatomy based on CT or MRI data.
High-resolution additive techniques ensure that these implants meet stringent dimensional and surface finish requirements, which are critical for integration with human tissue. Furthermore, porous structures can be incorporated directly into the design to promote osseointegration, where bone tissue grows into the implant, enhancing long-term stability.
Ceramic materials, particularly zirconia and alumina, are widely used in dental restorations such as crowns, bridges, and implants. With DLP-based ceramic printing, dental labs can now produce highly aesthetic, wear-resistant parts with micrometer-level accuracy. This not only accelerates production but also improves patient outcomes by ensuring a better fit and longer lifespan.
Beyond prosthetics and restorations, ceramic 3D printing is being explored for advanced applications such as drug delivery devices, microfluidic diagnostic chips, and scaffolds for tissue engineering—offering new frontiers for personalized medicine.
Automotive: Lightweighting and Rapid Tooling
The automotive industry, while traditionally slower in adopting additive manufacturing for end-use parts, is now increasingly integrating high-resolution metal and ceramic printing into its R&D, prototyping, and production workflows. Lightweighting remains a key driver, particularly in electric vehicles (EVs), where reducing mass translates directly into extended range and improved efficiency.
Topology-optimized components—such as suspension brackets, transmission housings, and heat exchangers—are now being printed in high-strength aluminum and titanium alloys with fine resolution and tight tolerances. This not only improves performance but also reduces the number of parts and fasteners, contributing to streamlined assembly lines and cost savings.
Rapid tooling is another compelling use case. High-resolution ceramic or metal inserts for injection molding, die casting, and stamping can be produced on-demand with internal cooling channels and surface textures tailored to specific applications. This significantly shortens tool development cycles, lowers tooling costs for low-volume runs, and enables iterative design improvements without disrupting production timelines.
In motorsports and high-performance automotive sectors, additive manufacturing is already proving indispensable. From custom engine components to aerodynamically optimized body parts, manufacturers are pushing the limits of what is possible with high-resolution 3D printed metals and ceramics.
Electronics: Precision in Miniaturized Components
In the electronics industry, the demand for smaller, faster, and more efficient devices necessitates components with extreme precision and complex geometries. High-resolution ceramic 3D printing is uniquely positioned to meet these demands by enabling the fabrication of substrates, insulators, and housing components with high dielectric strength and excellent thermal conductivity.
Advanced ceramics like alumina, aluminum nitride, and zirconia are essential for high-frequency applications, especially in telecommunications, microwave electronics, and sensor arrays. Traditional manufacturing techniques struggle with the miniaturization and intricate internal architectures required for next-generation devices. However, DLP and SLA-based ceramic printing now make it possible to produce these components at scale, with feature sizes below 100 microns and surface roughness in the nanometer range.
Additionally, metal 3D printing technologies are being used to fabricate connectors, shielding enclosures, and structural supports for printed circuit boards (PCBs). Innovations in multi-material additive manufacturing further allow for the integration of conductive pathways within ceramic or polymer matrices—paving the way for fully 3D printed electronic devices.
Defense and Energy: Durability in Extreme Conditions
Defense applications demand materials and manufacturing processes that can withstand extreme environments, including high temperatures, corrosive atmospheres, and intense mechanical stresses. High-resolution metal and ceramic 3D printing is rapidly becoming a strategic asset in this domain, enabling the creation of mission-critical components with unparalleled precision and performance.
For instance, advanced metal printing is used to fabricate turbine blades, propulsion components, and armored parts with optimized strength-to-weight ratios. The design freedom afforded by additive manufacturing also allows for internal cooling channels in missile and jet engine components, improving thermal management and operational lifespan.
In the energy sector, particularly in nuclear and renewable power, ceramic printing is being utilized to create heat exchangers, insulators, and reactor components capable of operating under high radiation and thermal loads. Alumina and silicon carbide ceramics, due to their chemical stability and high-temperature resistance, are particularly well-suited for such applications. The ability to manufacture these parts with tight tolerances ensures safe and efficient system operation.
Additive manufacturing also supports the decentralization of defense and energy supply chains by enabling on-site or near-site production of replacement parts, reducing downtime and dependency on complex logistics networks.
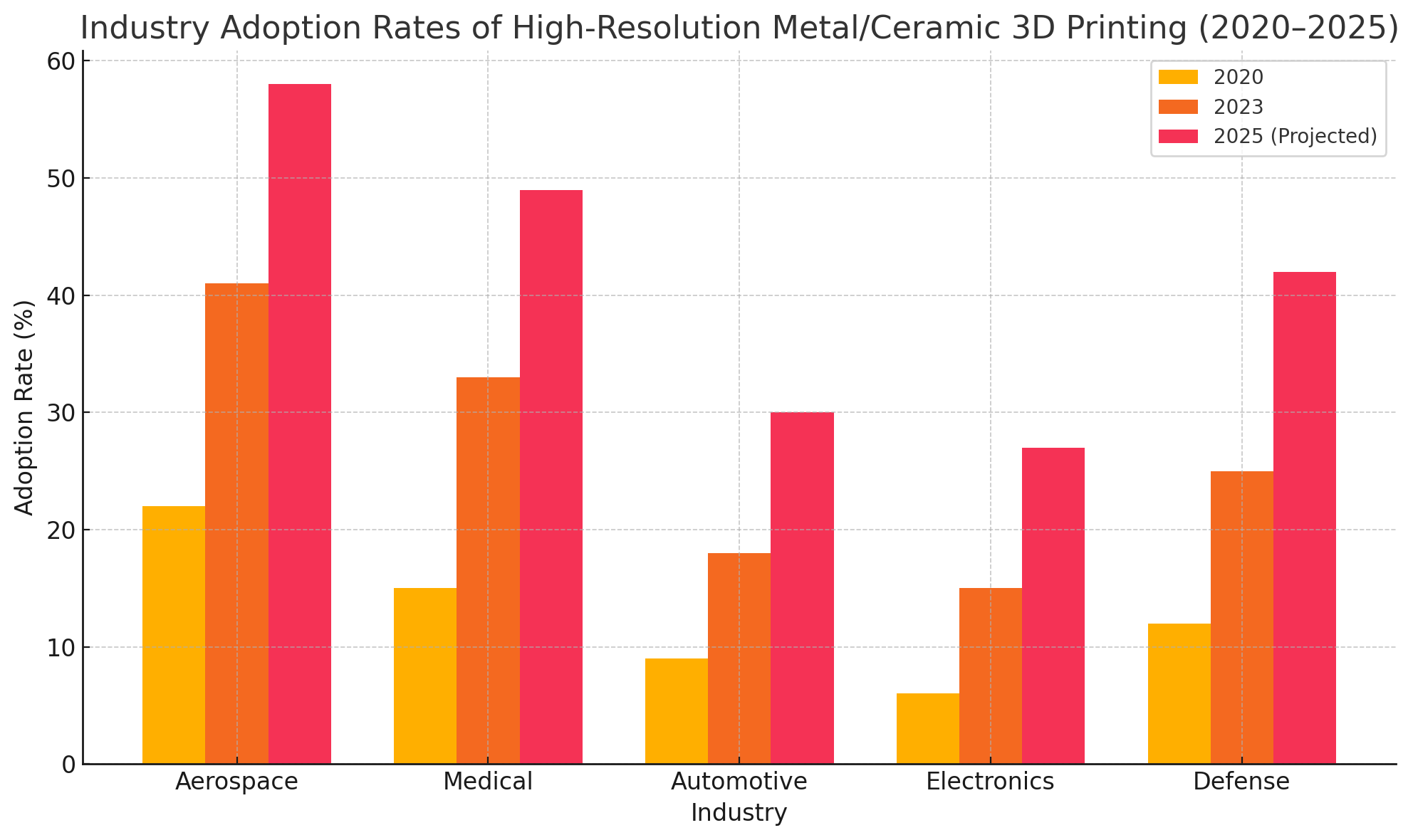
In conclusion, high-resolution 3D printing for metals and ceramics is catalyzing innovation across industries that demand precision, performance, and customization. Whether through lighter aerospace structures, biocompatible medical implants, or miniaturized electronic components, the technology is enabling capabilities previously constrained by traditional manufacturing methods. As costs continue to decline and material libraries expand, adoption will only accelerate, driving a new era of digital manufacturing across the global economy.
Economic and Sustainability Impacts
The integration of high-resolution 3D printing into industrial workflows is not only transforming the design and production of parts but also generating profound economic and environmental implications. As manufacturers seek to navigate increasingly competitive global markets, additive manufacturing presents a compelling value proposition—reducing costs, enabling agile production, and promoting sustainability. This section examines the cost-efficiency metrics and ecological advantages associated with the adoption of high-resolution 3D printing for metals and ceramics, as well as its role in supporting supply chain resilience and localized manufacturing strategies.
Cost Efficiency: From Prototyping to Production
One of the most immediate economic benefits of high-resolution 3D printing is its ability to eliminate the fixed tooling costs associated with traditional subtractive and formative manufacturing methods. In conventional production, especially for metals and ceramics, the design and fabrication of molds, dies, and jigs represent significant capital expenditures. These costs are particularly burdensome for low- to mid-volume production runs, where economies of scale are difficult to achieve.
High-resolution 3D printing removes the need for such tooling, allowing parts to be produced directly from digital designs. This is particularly advantageous in aerospace, medical, and defense sectors, where components are often custom, complex, and manufactured in limited quantities. Furthermore, design changes can be implemented rapidly without incurring additional tooling costs, thereby shortening product development cycles and reducing time to market.
While the material cost per kilogram for high-performance metals and ceramics used in additive manufacturing can be relatively high, these costs are often offset by the ability to minimize waste. Additive manufacturing is inherently more material-efficient than subtractive methods such as CNC machining, which can discard 70–90% of raw material in the form of chips and shavings. In contrast, 3D printing deposits material only where it is needed, significantly reducing scrap and raw material usage.
Moreover, the consolidation of multiple components into a single 3D-printed part not only streamlines assembly but also lowers inventory costs, reduces the need for fasteners and adhesives, and minimizes the risk of part failure due to joint fatigue. Collectively, these factors contribute to a leaner and more cost-effective manufacturing process.
Sustainability Gains and Environmental Responsibility
Beyond cost savings, high-resolution 3D printing aligns with broader environmental goals by reducing the ecological footprint of manufacturing operations. Traditional metal and ceramic manufacturing processes are energy-intensive and often involve hazardous chemicals or environmentally damaging byproducts. Additive manufacturing, when properly optimized, offers a cleaner alternative.
One key area of environmental benefit is material waste reduction. As mentioned, subtractive processes typically produce significant waste, especially when machining expensive metals like titanium or high-purity ceramics. Additive methods use only the required amount of material, with unused powder often recyclable for future prints—further enhancing sustainability.
Energy consumption also shifts favorably with additive manufacturing, particularly when production is localized. Instead of transporting raw materials and finished goods across continents, parts can be printed on-site or near the point of use, dramatically reducing carbon emissions associated with logistics. Additionally, optimized designs made possible by 3D printing often require less material overall, leading to lighter-weight parts that contribute to energy savings during the product's operational life—particularly in vehicles and aircraft.
Ceramic 3D printing, in particular, holds promise for creating components used in clean energy systems, such as high-efficiency heat exchangers and insulating components in renewable power applications. These parts contribute directly to more sustainable energy production, while the additive process itself reduces the environmental impact of manufacturing such advanced systems.
Agile Supply Chains and Localized Production
The COVID-19 pandemic underscored the fragility of global supply chains, prompting industries to reevaluate their reliance on centralized production hubs. High-resolution 3D printing offers a strategic advantage by enabling distributed and localized manufacturing. By digitizing inventory and producing parts on demand, organizations can significantly reduce lead times, avoid stockpiling, and respond swiftly to market changes or supply disruptions.
This decentralized model is particularly beneficial for remote locations, military operations, or space exploration missions, where access to conventional manufacturing facilities is limited. With high-resolution 3D printers and digital part libraries, critical components can be fabricated on-site, reducing dependency on extended logistics chains and improving operational readiness.
Furthermore, the ability to iterate quickly using additive manufacturing supports just-in-time production models, where goods are made as needed rather than forecasted in bulk. This reduces waste, lowers storage requirements, and enhances production responsiveness—leading to more efficient use of resources and capital.
Workforce Implications and Economic Upskilling
The adoption of high-resolution 3D printing also has implications for labor economics and workforce development. As manufacturing becomes increasingly digitized, new skill sets are required—ranging from CAD design and materials engineering to machine operation and post-processing. This shift presents both challenges and opportunities.
While some traditional manufacturing jobs may be displaced, the emergence of additive manufacturing technologies creates demand for highly skilled workers capable of designing for additive processes, maintaining sophisticated equipment, and ensuring quality control in a digital environment. Governments and educational institutions are beginning to respond with specialized training programs and certification pathways that prepare the workforce for these roles.
In the long term, the economic shift toward high-resolution 3D printing could contribute to regional revitalization, particularly in areas seeking to rebuild advanced manufacturing capabilities. By lowering barriers to entry and enabling flexible production, additive manufacturing empowers small and medium-sized enterprises (SMEs) to compete in high-value markets previously dominated by large incumbents with capital-intensive operations.
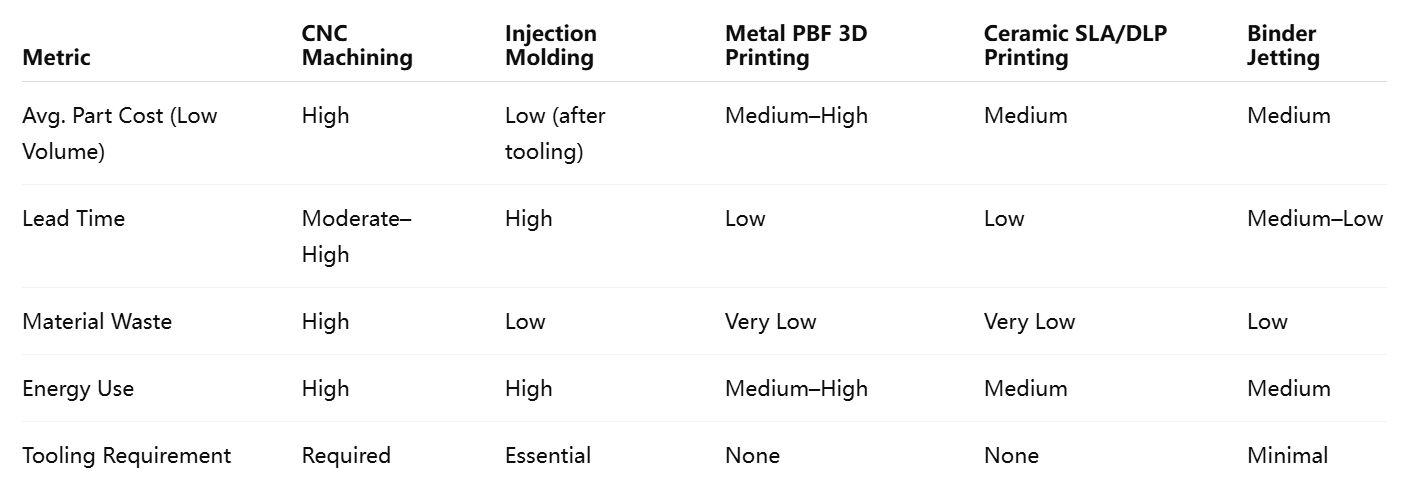
In summary, the economic and environmental advantages of high-resolution 3D printing for metals and ceramics extend well beyond the boundaries of cost reduction. By promoting material efficiency, enabling on-demand localized production, and supporting a highly skilled digital workforce, additive manufacturing contributes meaningfully to a more sustainable and resilient industrial ecosystem. As these technologies continue to advance, they are poised to play a central role in shaping the next generation of manufacturing—economically viable, environmentally responsible, and globally distributed.
Challenges and the Road Ahead
While high-resolution 3D printing for metals and ceramics holds immense promise and has demonstrated transformative potential across various industries, several challenges must be addressed before the technology can achieve widespread adoption at scale. These challenges span technical, economic, regulatory, and human factors. Understanding and overcoming them will be critical to unlocking the full value of this advanced manufacturing paradigm. This section explores the current limitations, ongoing innovations, and future trajectory of high-resolution additive manufacturing.
Material Limitations and Qualification Bottlenecks
A significant barrier to broader adoption is the limited availability and qualification of printable metals and ceramics. Unlike polymers, which can be easily extruded or cured, metals and ceramics require exacting specifications in terms of particle size, purity, and flow characteristics to be suitable for high-resolution additive manufacturing. Furthermore, each new material introduced into a printing platform must undergo extensive testing to validate its mechanical properties, microstructure stability, and performance under operational loads.
For mission-critical applications in aerospace, defense, and medical fields, qualification standards are especially rigorous. Certification processes for 3D-printed parts involve not only verifying that printed components meet dimensional tolerances and strength requirements but also ensuring repeatability and long-term reliability. These procedures are time-intensive and costly, often dissuading manufacturers from adopting new materials even when they present clear technical advantages.
Material science innovation will be key to resolving these constraints. Efforts are underway to develop new metal and ceramic powders with better sinterability, enhanced flow properties, and improved recyclability. Additionally, hybrid materials and functionally graded compositions—where different properties can be embedded within a single part—are on the horizon, though they add new layers of complexity in terms of process control and quality assurance.
Surface Finish and Post-Processing Demands
Despite advances in printing resolution, post-processing remains a critical step in the production workflow for high-resolution 3D-printed parts. As-printed surfaces, particularly in metal PBF processes, often exhibit roughness due to partially fused particles or stair-stepping artifacts caused by layer-by-layer deposition. These surface irregularities can impact fatigue life, wear resistance, and functional interfacing of mechanical parts.
In response, manufacturers typically employ techniques such as machining, polishing, shot peening, or chemical etching to improve surface quality. However, these steps can be time-consuming, introduce additional cost, and may negate some of the advantages of rapid digital manufacturing. Moreover, post-processing complex internal geometries or lattice structures—features that additive manufacturing is uniquely capable of producing—remains difficult or infeasible with conventional methods.
Automated, scalable solutions for post-processing are emerging but require further development to handle the diversity of part shapes and materials produced through high-resolution 3D printing. Innovations in support-free printing, self-polishing alloys, and in-situ surface finishing could help mitigate this dependency over the long term.
Standardization and Regulatory Compliance
Another critical challenge is the lack of universal standards governing high-resolution additive manufacturing processes, especially for metal and ceramic parts. Currently, manufacturers must navigate a patchwork of industry-specific guidelines and internal qualification protocols, leading to inefficiencies and inconsistent quality assurance practices.
Organizations such as ASTM International, ISO, and ASME are actively developing standards for additive manufacturing, but adoption is uneven and lags behind the pace of technological progress. For high-stakes industries—particularly medical and aerospace—regulatory bodies demand documentation of every step in the production process, from material sourcing and handling to build parameters and post-processing methods.
The absence of standardized data formats, part testing protocols, and inspection criteria complicates efforts to scale up production and establish interoperability across systems. This lack of harmonization poses a risk for companies seeking to expand operations globally or integrate additive manufacturing across multiple sites.
As the industry matures, standardized frameworks for digital thread management, quality control, and certification will be essential to build trust, ensure repeatability, and facilitate widespread adoption.
Talent Gap and Organizational Readiness
The successful implementation of high-resolution additive manufacturing depends not only on technology but also on human capital. The shift from traditional manufacturing to digitally enabled 3D printing demands new skills and cross-disciplinary knowledge. Designers must be trained in design for additive manufacturing (DfAM) principles; engineers must understand process parameters and machine calibration; operators need expertise in post-processing and part inspection.
Unfortunately, the current talent pool is not adequately equipped to meet this demand. A shortage of trained professionals slows deployment and limits the ability of companies to scale production effectively. In many cases, even well-resourced organizations struggle to integrate 3D printing into existing workflows due to resistance to change, lack of internal expertise, or misalignment between engineering and production departments.
Investment in education, workforce development, and collaborative partnerships between industry and academia will be critical. Training programs that blend theoretical knowledge with hands-on machine experience can help bridge the skills gap. Additionally, internal change management strategies will be necessary to align organizational culture with the agile, iterative nature of additive manufacturing.
The Future Trajectory: Toward Autonomous, Scalable Manufacturing
Looking ahead, the future of high-resolution 3D printing for metals and ceramics lies in greater automation, scalability, and integration with digital manufacturing ecosystems. Emerging trends include:
- Closed-Loop Process Control:
Real-time monitoring of build conditions, combined with machine learning algorithms, is enabling systems to self-correct during printing, thereby improving consistency and reducing defects. - AI-Driven Design Optimization:
Artificial intelligence is being used to generate complex geometries that maximize performance while minimizing material use—designs that are impractical or impossible to create manually. - Multi-Material Printing:
New systems are being developed to print multiple materials—including combinations of metals, ceramics, and polymers—in a single build. This opens possibilities for embedded sensors, graded structures, and functionally integrated devices. - Mass Customization and Digital Inventory:
As digital part libraries grow, companies can transition from physical inventories to on-demand production models. This enhances flexibility, reduces waste, and enables rapid customization without compromising cost-efficiency. - Sustainability as a Competitive Differentiator:
With mounting pressure to reduce carbon emissions and adopt circular manufacturing models, the sustainability advantages of additive processes will become increasingly central to strategic planning.
In conclusion, the road to mainstream adoption of high-resolution 3D printing for metals and ceramics is both promising and complex. Technological innovation must be matched by progress in standardization, workforce development, and integration into broader supply chains. While challenges persist, they are not insurmountable—and the momentum behind this transformative manufacturing approach continues to build.
As costs decline, materials diversify, and capabilities expand, high-resolution 3D printing is poised to become not just a complementary tool, but a cornerstone of next-generation manufacturing. Its ability to produce intricate, high-performance parts on demand, with minimal waste and unparalleled customization, positions it at the forefront of a new industrial era—one defined by agility, precision, and sustainability.
Precision Manufacturing for a New Industrial Era
High-resolution 3D printing for metals and ceramics is fundamentally reshaping the manufacturing landscape. By enabling the production of geometrically complex, lightweight, and high-performance parts, it offers a compelling alternative to traditional manufacturing methods—particularly in sectors where precision, durability, and customization are paramount. From aerospace and medical to automotive, electronics, and defense, the technology is driving innovation, enhancing efficiency, and enabling new product paradigms.
Despite existing challenges—including material qualification, post-processing demands, standardization hurdles, and workforce readiness—the trajectory of high-resolution additive manufacturing is clear. As the ecosystem matures, supported by advancements in artificial intelligence, real-time process control, and multi-material printing, the barriers to adoption are steadily diminishing.
Economically, the shift toward digital, on-demand production models is unlocking new efficiencies and reducing the reliance on capital-intensive tooling. Environmentally, the technology’s inherent material and energy efficiencies contribute to more sustainable manufacturing practices, aligning with global goals for carbon reduction and resource conservation.
In essence, high-resolution 3D printing is not merely an incremental improvement—it is a strategic enabler of next-generation manufacturing. Those who invest in its development today will be best positioned to lead the industrial transformation of tomorrow.
References
- GE Additive - Metal Additive Manufacturing Overview
https://www.ge.com/additive/additive-manufacturing/metal-additive-manufacturing - EOS - Metal 3D Printing Explained
https://www.eos.info/en/additive-manufacturing/metal - Desktop Metal - Bound Metal Deposition Technology
https://www.desktopmetal.com/products/studio - Lithoz - High-Precision Ceramic 3D Printing
https://www.lithoz.com/en/ceramic-3d-printing - XJet - Ceramic and Metal Additive Manufacturing
https://www.xjet3d.com - Velo3D - SupportFree Metal 3D Printing Technology
https://velo3d.com/technology/ - ASTM International - Additive Manufacturing Standards
https://www.astm.org/industry/additive-manufacturing-technology - NASA - 3D Printed Rocket Engine Components
https://www.nasa.gov/technology/3d-printed-rocket-engine-components - Ceramics Expo - Innovations in Ceramic Additive Manufacturing
https://www.ceramicsexpousa.com - MIT Technology Review - The Future of Additive Manufacturing
https://www.technologyreview.com/2023/03/01/the-future-of-additive-manufacturing/